ASTM A 106 Seamless Pipe
Home >
-
API steel pipe
- API steel pipe
- API steel casing pipe
- Casing and Tubing
- API drill pipe
- API5L steel pipe
- Oil pipeline

-
Carbon steel pipe
- Carbon steel pipe
- Welded steel Pipe
- seamless carbon steel pipe
- Petroleum Casing Pipe

-
Alloy steel pipe
- astm a 335 gr p22
- alloy steel pipe l555
- 25crmo4 alloy steel pipe
- alloy pipe a335 p11








- interpret seamless steel pipe
- Water pipeline - Handling and
- Applications of welded pipe pil
- welded steel pipes and Seamless
- ASTM A 106 Seamless Pipe
- Carbon dioxide resistant oil ca
- seamless steel pipe On-line col
- EN 10305-1 / DIN 2391 cold draw
- EN 10255 Standard Pipe,replaces
- API 5L A53 / A106 Grade B, Seam
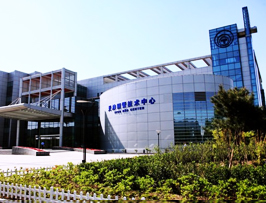
One of the Top 500 enterprises in China foreign trade
QCCO was approved as a member of “China Association for Contracting Projects Abroad “and granted a membership certificate on Sep 28,2005; “Credibility Rating AAA certificate in Foreign Trade” was granted to QCCO by China Shippers’ Association
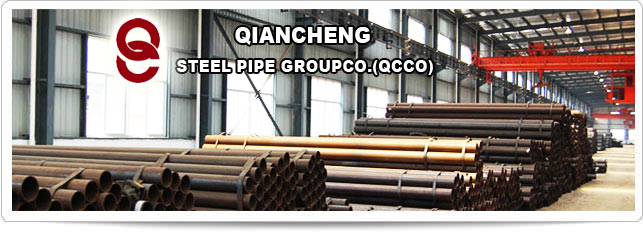
Scope
Covers seamless carbon steel Grades A & B pipe for high pressure and high temperature service. Pipe is suitable for bending, flanging, and similar forming operations and for welding. Applications include: Refineries, Power Plants, Boilers, Ship Building, and other specialized applications.
Heat Treatment
Hot-finished pipe need not be heat treated. Cold-drawn pipe shall be heat treated after the final cold draw pass at a temperature of 1200°F or higher.
Hydrostatic & Nondestructive Electric Testing
Hydrostatic inspection test pressure is 2500 psi for sizes NPS 2 and under. Test pressure shall be maintained for a minimum of 5 seconds.
When specified by the purchaser, pipe may be tested by the nondestructive electric test in lieu of the hydrostatic test.
End Finish Plain End:
NPS 1-1/2 and smaller shall be either plain end square cut or plain end beveled at the option of the manufacturer. NPS 2 ends shall be beveled to angle 30° +5°, -0° with a root face of U16” 土 1/32”.
Threaded Pipe:
Threads comply with ANSI Standard B 1.20.1
Couplings:
Couplings comply with ASTM Standard A 865 Available Coatings
ASTM A 106 seamless pipe is available in four different coatings:
• Exclusive Blue Diamond® Coating
• Hot-Dipped Galvanized
• Pickled and Oiled
• Bare
Chemical Requirements Composition, % Max
CarbonA Manganese Phosphorus Sulfur .25 0.27/0.93 .035 .035
Silicon CopperB NickelB ChromiumB 0.10 Min .40 .40 .15
MolybdenumB VanadiumB
.15 .08
AFor each reduction of 0.01% below the specified carbon maximum, an increase of 0.06% manganese above the specified maximum will be permitted up to a maximum of 1.35%
BThe combination of these five elements shall not exceed 1.00%
Tensile Requirements
Yield Strength, min 35,000 psi Tensile Strength, min 60,000 psi Elongation in 2” 35% Minimum
Bending Test (Cold) For NPS 2 and under
Degree Diameter of Mandrel
Of Bend
Standard 90° 12 X pipe O.D.
Close Coiling 180° 8 X pipe O.D.
Frequency of Tests
Tensile tests and flattening tests are required on one length of pipe from each lot of 400 lengths or fraction thereof for each size.
Dimensions and Weights
The dimensions and weights furnished under this specification are in agreement with the standardized dimensions and weights specified in ANSI B 36.10.
Plain End Dimensions Schedules 40 & 80
Schedule 40 | Schedule 80 | ||||
Nominal
Size |
O.D.
Inches |
Wall |
Weight,
Lb/Ft |
Wall |
Weight,
Lb/Ft |
1/8 | 0.405 | .068 | 0.24 | .095 | 0.31 |
1/4 | 0.540 | .088 | 0.43 | .119 | 0.54 |
3/8 | 0.675 | .091 | 0.57 | .126 | 0.74 |
1/2 | 0.840 | .109 | 0.85 | .147 | 1.09 |
3/4 | 1.050 | .113 | 1.13 | .154 | 1.48 |
1 | 1.315 | .133 | 1.68 | .179 | 2.17 |
1-1/4 | 1.660 | .140 | 2.27 | .191 | 3.00 |
1-1/2 | 1.900 | .145 | 2.72 | .200 | 3.63 |
2 | 2.375 | .154 | 3.66 | .218 | 5.03 |
Schedule 160 | Schedule XXS | ||||
Nominal
Size |
O.D.
Inches |
Wall |
Weight,
Lb/Ft |
Wall |
Weight,
Lb/Ft |
1/8 | 0.405 | N/A | N/A | N/A | N/A |
1/4 | 0.540 | N/A | N/A | N/A | N/A |
3/8 | 0.675 | N/A | N/A | N/A | N/A |
1/2 | 0.840 | .188 | 1.31 | .294 | 1.72 |
3/4 | 1.050 | .219 | 1.95 | .308 | 2.44 |
1 | 1.315 | .250 | 2.85 | .358 | 3.66 |
1-1/4 | 1.660 | .250 | 3.77 | .382 | 5.22 |
1-1/2 | 1.900 | .281 | 4.86 | .400 | 6.41 |
2 | 2.375 | N/A | N/A | N/A | N/A |
Permissible Variations in Wall Thickness
Minimum wall thickness at any point shall not be more than 12.5% under nominal wall thickness specified. Maximum wall thickness at any point shall not be greater than 20.0% over nominal wall thickness.
Workmanship
Visual imperfections such as scabs, seams, laps or tears shall not exceed 5% of the nominal wall thickness.
Permissible Variations in Outside Diameter
NPS 1-1/2 and under ±1/64”
NPS 2 ±1/32”
Permissible Variations in Weight per Foot
Pipe shall not vary more than 10% over and 3.5% under the standard specified.
Product Marking
Each length of pipe is continuously stenciled to show the manufacturer, specification (A106), size (O.D. & wall), “A & B” for Grades A & B, 2500 psi, length and heat number
Manufacturing Location
All product furnished by Wheatland Tube
Company and Sharon Tube Company are
manufactured by Sharon Tube in Sharon, PA,
USA.
Hot-Dipped Galvanized
Pipe is galvanized to the requirements of ASTM A 53. The average weight of zinc coating shall not be less than 1.8 ounces per square foot of surface (inside and outside).
When galvanized pipe is bent or otherwise fabricated to a degree that causes the zinc coating to stretch or compress beyond the limit of elasticity, some flaking of the coating may occur.
上一篇:seamless steel pipe production and trade data - European