Boiler steel pipe hydrostatic testing and eddy current testi
Home >
-
API steel pipe
- API steel pipe
- API steel casing pipe
- Casing and Tubing
- API drill pipe
- API5L steel pipe
- Oil pipeline

-
Carbon steel pipe
- Carbon steel pipe
- Welded steel Pipe
- seamless carbon steel pipe
- Petroleum Casing Pipe

-
Alloy steel pipe
- astm a 335 gr p22
- alloy steel pipe l555
- 25crmo4 alloy steel pipe
- alloy pipe a335 p11








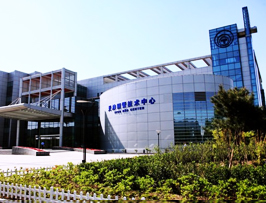
One of the Top 500 enterprises in China foreign trade
QCCO was approved as a member of “China Association for Contracting Projects Abroad “and granted a membership certificate on Sep 28,2005; “Credibility Rating AAA certificate in Foreign Trade” was granted to QCCO by China Shippers’ Association
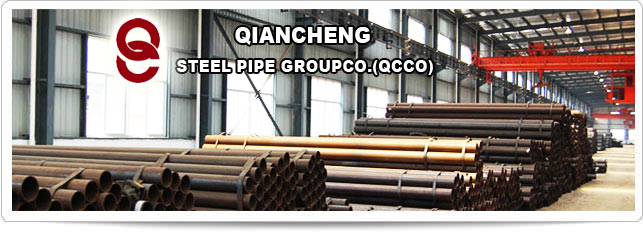
ASTM A179/(ASME SA179) Boiler steel pipe
Seamless Cold Drawn Low Carbon Steel Boiler steel pipe

Application: | |||||
For tubular heat exchangers,condensers,and similar heat transfer apparatus. | |||||
Size(mm): | O.D.:6.0~114.0 W.T.:1~15 L:max 12000 | ||||
Grade and Chemical Composition (%) | |||||
Chemical Composition | C | Mn | P≤ | S≤ | Si≤ |
0.06-0.18 | 0.27-0.63 | 0.035 | 0.035 | 0.25 | |
(SA-450/SA-450M): | |||||
OD In (mm) | + | - | WT In(mm) | + | - |
<1(25.4) | 0.1 | 0.1 | ≤1.1/2(38.1) | 20% | 0 |
1~1.1/2(25.4~38.1) | 0.15 | 0.15 | >1.1/2(38.1) | 22% | 0 |
>1.1/2~<2(38.1~50.8) | 0.2 | 0.2 | |||
2~<2.1/2(50.8~63.5) | 0.25 | 0.25 | |||
2.1/2~<3(63.5~76.2) | 0.3 | 0.3 | |||
3~4(76.2~101.6) | 0.38 | 0.38 | |||
>4~7.1/2(101.6~190.5) | 0.38 | 0.64 | |||
>7.1/2~9(190.5~228.6) | 0.38 | 1.14 |
|
A boiler steel pipe quality problems
Boiler seamless steel pipe (hereinafter referred to as boiler pipe) is an important manufacturer of boiler materials , its quality is directly related to how the boiler manufacturing quality so that installation quality and quality in use. Boiler quality steel should be made Steel Plant to make guaranteed, but in the case of short supply, available to boiler tube boiler factory used always found some quality problems, it is made of boiler pressure parts as major Wall tube, convection tubes, superheater tubes, heat exchanger tubes leaking or burst pipes phenomena have occurred, has become plagued boiler quality of a big problem, this boiler manufacturers and users have a great view. In the case of a seller's market, the boiler manufacturer almost assume full responsibility, including material suppliers including; how to control the quality of the boiler tube boiler manufacturer has now become an issue of growing concern, the solution is nothing more than two ratings: one for boiler tube-by-roots pressure test ; the other is the implementation of the boiler tube 100% of eddy current testing.
Boiler steel pipe hydrostatic testing and eddy current testing - equally steel eddy current test denseness
Our GB5310-85 and YB ( T ) 32-86 standard very clearly states: "Where the pipe through the eddy current testing, hydrostatic testing can not do." This is because the eddy current testing is also a kind of material density test, it hydrostatic test are equivalent. German steel test specification SEP1925-74 "steel vortex density test," said: "Eddy current testing is a compact test, use it instead of the hydrostatic test - the provisions of various shapes within the hollow body of the hydrostatic test pressure." Why eddy current testing is also a compact test it? Starting from the basic principles which have to eddy current flaw detection.
An eddy current detection principle:
Eddy Current Testing ( ET ) is one of the conventional non-destructive testing technology, which is suitable for conductive materials such as ferromagnetism and profiles and parts and graphite products to detect non-ferromagnetic, and can find cracks, folding, pits, inclusions, osteoporosis and other surfaces and near-surface defects, can usually determine the location of defects and the relative size , but it is difficult to judge a type of defect. Eddy current testing in the profile (such as pipes, rods, wires) of testing, material sorting, thickness measurement, determination of the physical properties of the specimen and other aspects of a wide range of applications.
Eddy current testing is based on the theory of electromagnetic induction, a simple eddy current testing system includes a high-frequency AC voltage generator, a detection coil and an indicator. High-frequency voltage generator (or oscillator) with excitation current detection coil supply, resulting in the specimen (pipe) and formed around an excitation field, the magnetic field induces a current in the swirling vortex called the specimen; test parts of the vortex and generates its own magnetic field, eddy magnetic excitation field weakening or against the cut, resulting in changes in the magnetic field. This change depends on the distance between the coil and the pipe and, pipe geometry, conductivity and magnetic permeability, and pipe metallurgy and mechanical defects. When the pipe through the coil, due to changes in parameters of these pipes, causes a change in the electromagnetic effects and generates an electrical signal, the signal is amplified and converted, alarm, recording and sorting, the final reachable pipe testing purposes.
2 , the skin effect and the skin depth
Direct current flowing in the conductor, which conductor the current density distribution in the cross-section substantially uniform, but when alternating current flows in the conductor, which current distribution in the conductor is non-uniform cross-section. The maximum current density of the surface layer, the more into the center conductor with increasing distance from its current distribution and concentration of surface decay, this phenomenon is called the skin effect of alternating current.
AC current density distribution in the cross section of the conductor is exponentially decays, namely:
|
Where: I O - surface current density, Amps / m 2 ; I - δ at depth from the surface current density, A / m 2 ; permeability μ-- conductor, Henry / m; σ-- conductor The conductivity, 1 / ohm meter; f - frequency, Hz; δ-- skin depth, m; bottom e-- natural logarithms, e = 2.718 ......; |
Skin Effect size is the skin depth δ will be described, i.e., to reduce the current density to the surface current density 1 / e = 37% density, that is: when the I / I O = I / e = e -1 when, then |
|
The above formula shows that the skin depth δ is the frequency f is inversely proportional to the square root, f is δ the greater the smaller. Eddy Current Testing, conductivity and permeability of the workpiece is unchanged, the only change is the frequency of the excitation current, and therefore, by changing the frequency of the current can be detected defects at different depths. |
In actual eddy current testing, testing process because of the need, the type of physical meaning vary. The magnetic permeability μ with respect to the conductors of the magnetic permeability mu r represent, if after the saturation magnetization by a ferromagnetic material, mu r ≈ 1 ; ac line frequency f with the excitation frequency f d represents; conductivity conductor with specimens conductivity σ, the unit changed to 1 / micro-ohm-cm, or with the resistivity of the specimen P , said, P = 1 / sigma . At this time, eddy current testing of standard skin depth d can be expressed as: |
|
For example: GB3087-82 standard 20 gauge steel Phi 51 × 3 pipe, made of low carbon steel, Table shows that P = 16.9 (.cm); if using 5KHz excitation frequency detection in theory thickness : |
|
Seen from the theoretical calculation, when the above testing process, Phi 51 × 3 all are within the steel pipe wall thickness of the effective detection range of the detection, not missed theory. |
3 , the end effect |
Eddy Current Testing, due to (edge) drastically changed the geometry of the workpiece caused by magnetic and eddy adjacent sides interference will mask the detection of a range of defects. This phenomenon is called the end effect. Due to the presence of end effect, when the steel pipe testing, when the end of the tube (head and tail) entering or leaving the detection coil, located close to the defect for the pipe ends, will lose sensitivity, the tube ends are usually exist some blind area. Therefore, the entire root pipe eddy current inspection is carried out, the production process is the first on the eddy current inspection, after cutting pipe cutting. |
4 , eddy current testing coil |
Eddy current flaw detection coil sensor, its main role is to: establish a magnetic field in the wire piece, excited eddy current testing information transfer. There are three basic forms of detection coil: through type, style and point interpolation. Encircling coil surrounds the outside of the workpiece is detected, allowing free passage in which the workpiece. Pipe testing is used mainly through the ceremony. This coil is more suitable for rapid automated detection, it can also be used with steel coils point relative spiral motion. |
It should be noted that the eddy current flaw detection sensitivity is increased as the depth of burial of defects (or coil and the test piece gap) decreases. In order to improve the detection sensitivity should be to minimize the gap between the coil and steel, but if the gap is too small to prevent the pipe line through the circle of freedom, or damage to the coil. The gap between the coil and pipe sizes are available through the coil the filling factor η to indicate that it is the ratio of the cross-sectional area of the specimen and measuring the effective area of the coil, usually considered η≥ 0.7 . |
5 , eddy current testing the sensitivity of detection of defects |
China's national standard GB7735-87 "steel pipe eddy current testing method" is the standard applicable to the boiler, shipbuilding, petroleum, chemicals and other equipment with a circular eddy current testing of seamless steel tubes. When the standards for the whole surface of the pipe inspection, using through the coil, steel probe is not greater than the maximum outer diameter 180mm , artificial defects using drilling. |
Because of eddy current testing method is not an absolute measurement of the depth of the defect, but a relative detection mode, which is the result of the judgment of the testing of the sample by means of artificial defect contrast and natural defect display signal amplitude comparison method that is equivalent comparison method to determine the pipe defects. Artificial defect shape into two, one is the hole through the wall and perpendicular to the pipe surface. The other is parallel to the longitudinal axis of the steel pipe and the side parallel notches. Drilling artificial defects can best simulation steel surface pits, short and severe blistering and transverse cracks and other defects or injuries, so to replace the hydrostatic test of eddy current testing use more drilling artificial defects. The notch defect is able to simulate natural draw vertical cracks and other defects. |
Comparative sample preparation required, steel comparison sample probe should be the same nominal size of steel, chemical composition, surface condition, and when the pipe eddy current inspection heat treatment status similar to that have similar electromagnetic properties. Pipe curvature ( straightness ) should be less than 1.5 ‰, no surface oxide, and the length should be able to meet the requirements of testing equipment. www.steelpipechn.com Artificial defect on the comparative sample five, three in the middle portion of the comparative sample, mutually circumferentially spaced 120 °, inter-axis distance between each other is not less than 200mm , from the two ends of not more than 200mm to test the end effect. |
Thus, as long as eddy current testing process the right way, for the thin-walled steel pipe, it is a variety of defects can be detected in the presence of metal section thickness, it can be said that the steel pipe eddy current testing is also a dense material test, and hydrostatic testing of steel tubes equivalence. GB7735-87 standards: A class is suitable for hydraulic test instead. |